Heating, Ventilation, and Air Conditioning (HVAC) systems are critical components in pharmaceutical manufacturing facilities. These systems not only ensure the comfort and safety of personnel but also maintain controlled environmental conditions required for the production of high-quality pharmaceutical products. Proper design, installation, and maintenance of HVAC systems are essential to comply with Good Manufacturing Practices (GMP) and ensure product quality.
This article provides a comprehensive overview of HVAC systems in pharmaceutical sites, including design principles, operational requirements, maintenance protocols, and the role of HVAC in ensuring GMP compliance.
Importance of HVAC Systems in Pharmaceutical Facilities
HVAC systems serve three primary purposes in pharmaceutical facilities:
Environmental Protection: Limit the release of dust, fumes, and vapors into the external environment, complying with local and international regulations.
Product Protection: Prevent contamination by controlling airborne particulates, microorganisms, and humidity levels.
Personnel Protection: Provide a safe and comfortable working environment, especially when handling hazardous substances.
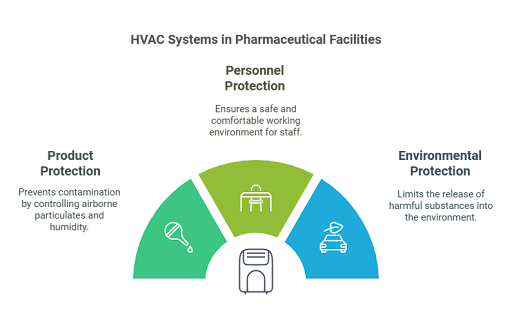
Design Considerations
- Air Quality and Filtration:
HVAC systems are designed to achieve specific cleanroom classifications, as per ISO 14644 standards. HVAC systems use various types of filters to meet specific environmental requirements.
Varies, depends on the contaminant | Efficiency | Filter Class (EN 779 & EN 1822) | Typical Application | Advantages | Disadvantages |
Primary Filters | 40-60% (large particles) | G1 to G4 | Initial filtration for removing larger particulates (e.g., dust, pollen). | Inexpensive, long service life. | Limited efficiency for finer particles. |
Secondary Filters | 80-95% (medium particles) | F5 to F9 | Removes harmful chemical vapors or fumes from the air. | Enhances HEPA filter lifespan. | Higher resistance than primary filters. |
HEPA Filters | 99.97% (≥0.3 microns) | H13 to H14 | Pre-filtration before HEPA filters reduces the load on final filters. | High filtration efficiency, GMP compliant. | Expensive, requires careful maintenance. |
ULPA Filters | 99.999% (≥0.1 microns) | U15 to U17 | Ultra-high cleanroom applications, e.g., aseptic processing. | Highest efficiency, suitable for sterile areas. | Very high cost, higher airflow resistance. |
Activated Carbon Filters | Cleanrooms and controlled areas are used to remove fine particulates, microorganisms, and airborne contaminants. | Not classified (absorption-based) | Removes odors, fumes, and chemical vapors. | Effective for gaseous contaminants. | Limited application for particulates. |
Chemical Filters | Specific to the chemical type | Not classified | Removes harmful chemical vapors or fumes from air. | Customized for specific chemicals. | Costly, needs regular replacement. |
Comparison between the different types of filters used in HVAC
2. Temperature and Humidity Control:
Maintain stable temperature and relative humidity to prevent product degradation and ensure process consistency. Use dehumidifiers, chemical dryers, or refrigerated coils to achieve low-humidity environments where necessary.
3. Airflow and Pressure Differentials:
Controlled airflow patterns (unidirectional or turbulent) ensure efficient particle removal and maintain cleanliness levels. Pressure cascades prevent cross-contamination by maintaining higher pressures in cleaner zones.
4. Room Classification and Air Changes:
Cleanrooms are classified based on cleanliness levels achieved under “As-built”, “At-rest”, and “Operational” conditions. Air changes per hour (ACPH) typically range from 6 to 20, depending on the cleanroom class and process requirements. ISO 14644-1 defines cleanroom classes based on the allowable particle concentration per cubic meter of air. The particle sizes measured are typically ≥0.1 μm, ≥0.5 μm, and ≥5.0 μm.
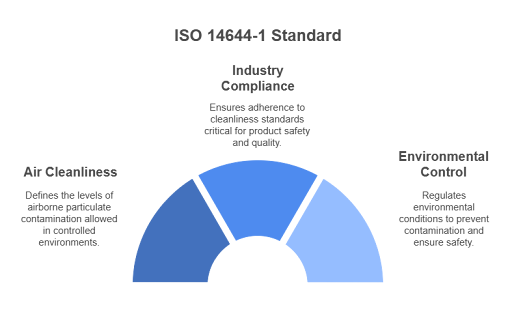
ISO Class | Particles per m³ (≥0.1 μm) | Particles per m³ (≥0.5 μm) | Particles per m³ (≥5.0 μm) | Typical Applications |
ISO 1 | 10 | Not defined | Not defined | Semiconductor manufacturing |
ISO 2 | 100 | Not defined | Not defined | Advanced electronics |
ISO 3 | 1,000 | 35 | Not defined | Aseptic processing in pharma |
ISO 4 | 10,000 | 352 | Not defined | Optical lens assembly |
ISO 5 | 100,000 | 3,520 | 29 | Sterile drug manufacturing (Grade A) |
ISO 6 | 1,000,000 | 35,200 | 293 | Sterile support areas (Grade B) |
ISO 7 | Not defined | 352,000 | 2,930 | Non-sterile manufacturing (Grade C) |
ISO 8 | Not defined | 3,520,000 | 29,300 | Packaging areas (Grade D) |
ISO 9 | Not defined | Room air at ambient conditions | Room air at ambient conditions | Uncontrolled areas |
ISO standards
HVAC Components and Their Roles
- Air-Handling Units (AHUs):
Centralized systems that condition and distribute air throughout the facility. Key components include:
- Fans: Circulate air within the system.
- Cooling/heating coils: Regulate temperature.
- Filters: Remove contaminants.
- Humidifiers/dehumidifiers: Control moisture levels.
To read more about each component: https://pharmaguddu.com/pharmaceutical-ahu-and-hvac-components/
- Ductwork:
- Designed to minimize contamination risks and ensure efficient airflow.
- Constructed from non-shedding materials to prevent particulate release.
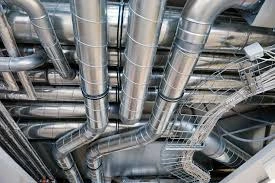
To read more about Ductwork: https://pharmacistpk.com/standards-and-types-of-hvac-ductwork-in-the-pharmaceutical-industry/
Type | Material | Advantages | Disadvantages | Applications |
Rigid Ductwork | Steel, Aluminum | Durable, efficient airflow, low leakage | Higher cost, requires space for installation | Cleanrooms, high-pressure systems |
Flexible Ductwork | Metal, Plastic | Easy to install, lightweight | Prone to sagging, higher leakage | Secondary connections, tight spaces |
Pre-Insulated Ductwork | Foam panels, Aluminum | Lightweight, energy-efficient | Limited strength, less durable | Energy-efficient HVAC systems |
Fabric Ductwork | Synthetic Fabric | Uniform airflow, easy maintenance | Limited durability, not suitable for high pressure | Non-critical areas, low-contamination zones |
Double-Wall Ductwork | Metal with Insulation | Excellent insulation, noise reduction | Expensive, bulky | Noise-sensitive or temperature-critical areas |
Comparison between different types of Ductwork
- Dampers and Diffusers:
- Dampers control airflow volume and direction.
- Diffusers ensure uniform air distribution and minimize turbulence.
How to choose a suitable diffuser https://www.pharmaguideline.com/2013/09/different-types-of-diffusers-hvac-system.html
- Control Systems:
- Automated systems monitor and regulate HVAC parameters such as temperature, humidity, and pressure.
- Examples include Building Management Systems (BMS) and Supervisory Control and Data Acquisition (SCADA) systems.
Cross-Contamination Prevention
- Pressure Cascade Systems:
- Ensure airflow from higher-pressure clean areas to lower-pressure less-clean areas.
- Typical pressure differentials range from 5 Pa to 20 Pa, depending on the criticality of adjacent zones.
- Airlocks:
- Personnel Airlocks (PAL) and Material Airlocks (MAL) prevent contamination during transitions between areas of differing cleanliness levels.
- Equipped with interlocked doors and appropriate ventilation.
- Filtration and Exhaust Systems:
- Recirculated air passes through HEPA filters to prevent contamination.
- Exhaust systems with adequate filtration handle dust, fumes, and hazardous vapors.
HVAC System Qualification and Validation
- Design Qualification (DQ): Verifies that the HVAC system design meets user requirements and GMP standards.
- Installation Qualification (IQ): Ensures that HVAC components are installed according to specifications and validated designs.
- Operational Qualification (OQ): Confirms that the system operates as intended under all anticipated conditions.
- Performance Qualification (PQ): Demonstrates consistent performance within defined parameters during normal operations.
- Testing and Documentation: Airflow visualization using smoke tests. Particle count measurements. Pressure differential and recovery time tests.
Maintenance and Energy Efficiency
- Preventive Maintenance:
- Regular inspections and filter replacements.
- Calibration of sensors and control systems.
- Energy-Saving Measures:
- Use variable frequency drives (VFDs) for fan motors.
- Optimize air changes and reduce airflow during non-production hours.
- Implement heat recovery systems to recycle energy from exhaust air.
- Documentation and Training:
- Maintain detailed records of maintenance activities.
- Train personnel in HVAC operation and troubleshooting.
Conclusion
HVAC systems are indispensable in pharmaceutical manufacturing, ensuring compliance with GMP standards and safeguarding product quality. By understanding the principles of HVAC design, operation, and maintenance, pharmaceutical facilities can minimize risks associated with contamination, optimize energy use, and maintain high standards of production.
Through adherence to guidelines such as the WHO’s HVAC standards, manufacturers can achieve robust systems that support consistent, high-quality output while meeting regulatory requirements.